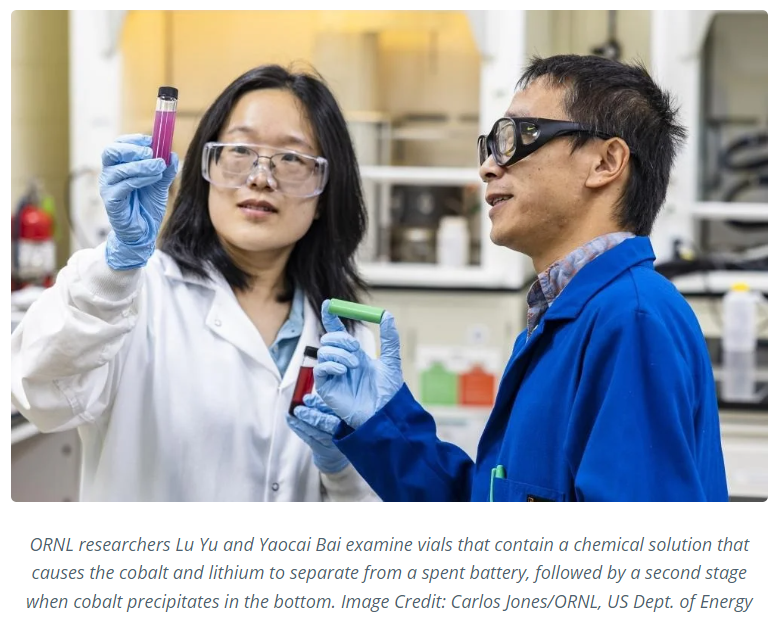
Discarded lithium-ion batteries originating from cell phones, laptops, and the increasing prevalence of electric vehicles are accumulating rapidly. However, viable recycling solutions for these batteries are largely confined to either burning them or chemically dissolving shredded batteries.
resently, these state-of-the-art methods come with potential environmental implications and are proving to be challenging to implement economically on an industrial scale.
The traditional method for recycling lithium-ion batteries yields only a small portion of the battery materials and heavily depends on corrosive, inorganic acids and hazardous chemicals, potentially introducing impurities into the process.
Furthermore, it involves complex procedures for separating and precipitating the crucial metals. Yet, reclaiming metals like cobalt and lithium holds promise for reducing pollution and lessening dependence on foreign sources and constrained supply chains.
Scientists at the Department of Energy’s Oak Ridge National Laboratory have made advancements in methods involving the dissolution of batteries in a liquid solution. Their improvements aim to curtail the use of hazardous chemicals within the recycling process.
ORNL researchers have devised a straightforward, effective, and eco-conscious remedy that surpasses prior challenges encountered by earlier methods.
They immerse the used battery in a solution containing organic citric acid, derived naturally from citrus fruits, dissolved in ethylene glycol—an antifreeze agent found in various consumer items such as paint and cosmetics. Citric acid, sourced sustainably, proves significantly safer to manage compared to inorganic acids. This environmentally-friendly solution demonstrates an impressively efficient technique for separating and retrieving metals from the positively-charged electrode, known as the cathode, within the battery.
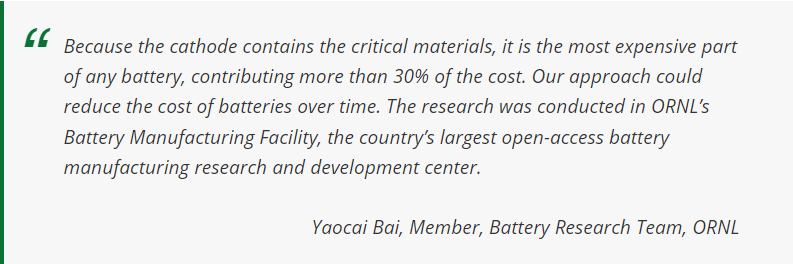
Their recycling method successfully extracted close to 100% of the cobalt and lithium from the cathode without introducing any impurities. Additionally, it facilitated a streamlined separation of the metal solution from other residues. Notably, it served a dual purpose by swiftly recovering over 96% of the cobalt within hours, eliminating the customary need to add additional chemicals to manually regulate acid levels—a typically intricate step in the process.
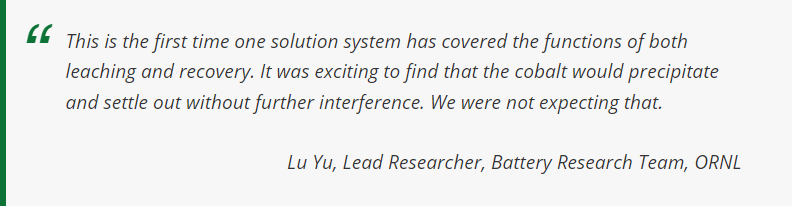
Eradicating the requirement for additional chemicals lowers costs and prevents the generation of byproducts or secondary wastes.
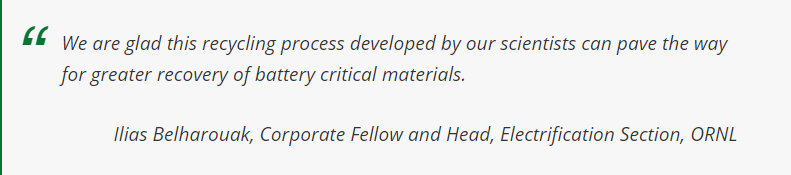
Bai adds, “The leaching performance of citric acid and ethylene glycol has been explored before, but that approach used more acid and a lower temperature, which proved less effective. We were surprised by how quickly the leaching happened in our solution. With an organic acid, it usually takes 10-12 hours, but this took only one.”
Traditional methods employing inorganic acids are slower due to the inclusion of water, which imposes limitations on the reaction temperature because of its boiling point.
This study was funded as a project of the Advanced Battery Recycling Consortium, or ReCell, a program of the Vehicle Technologies Office within DOE’s Office of Energy Efficiency and Renewable Energy. Yu, Bai, Belharouak, and scientists Rachid Essehli and Anuj Bisht donated to the research, which used the DOE’s Center for Nanophase Materials Science at ORNL.
Article Credit: azocleantech