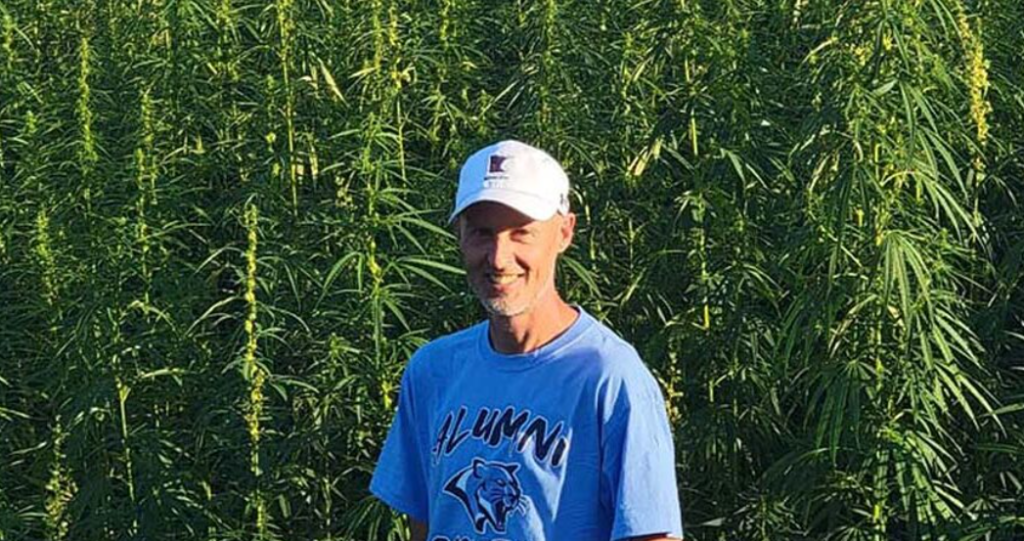
Commonly known as the plant behind the growing CBD market, hemp could someday have an entirely different role as a more sustainable insulation material.
Located two hours southwest of the Twin Cities near Morton, the Lower Sioux Indian Community is one of the national leaders in testing and using “hempcrete,” a plant-based replacement for typical insulation. A few years ago, tribal leaders wanted to create more employment opportunities for its more than 1,100 members and decided to pursue developing a growing, processing and building system for hempcrete.
Danny Desjarlais, the tribe’s hemp construction project manager, has been constructing homes with “hempcrete,” a mix of slivers of industrial hemp, water, lime binders, and other ingredients.
Hempcrete “gets rid of all of the toxic materials — the plastics and the different glues, latexes and petrochemicals — that we put into our wall system right now,” he said. “They all get replaced with hempcrete.”
Hempcrete has been installed in about 100 new and retrofitted homes in the United States, including five new homes on the reservation built by Sioux craftspeople. One, a duplex, is the first multifamily hempcrete-insulated home ever built in the country. The tribe, part of the Mdewakanton Band of Dakota, is also building a $6.2 million, 20,000-square-foot campus to process and store hurd, the part of industrial hemp used in hempcrete.
Desjarlais and his team have captured national attention, and Patagonia’s film division will feature him and his crew in a documentary. “Danny and his team have been able to deliver on one statement, and that statement is hemp is possible,” said U.S. Hemp Building Association President Ray Kaderli.
The hemp industry
Hemp had been legally grown in the United States before being effectively banned in 1937, and laws were loosened and then tightened again during the war on drugs. The 2018 federal farm bill created a regulated market that producers of tetrahydrocannabinol (THC) and cannabidiol (CBD) initially first exploited with a wide range of products. Other companies made hemp clothing, rope, food additives and other materials for the construction industry.
Industrial hemp, which uses a different hemp variety than CBD, is seen as the next emerging U.S. market, said Kaderli. He pointed to several encouraging trends, from the inclusion of hempcrete in the 2024 International Building Code to government research support and increased client interest.
A real estate broker and investor, Kaderli has built a few homes with hempcrete and likes its environmental performance attributes. It’s a natural insulator that could shave 30% to 60% off utility bills, Kaderli said. As hempcrete takes off, he believes hemp will eventually become a common rotational crop just like corn or soybeans.
Jean Lotus, editor of HempBuild Magazine, added that the United States is behind Europe, and especially France, where hemp has been used as a construction material for more than three decades. Members of the Northeast Bio-Based Materials Collective in Boston have embraced hempcrete and could begin incorporating it into projects, she said.
The Midwest had a strong tradition as a hemp supplier when it was legal, led by Wisconsin and Iowa, Lotus said. Today around 20 processors handle the nation’s industrial hemp, but she believes the numbers will grow as builders and their clients continue to explore decarbonization strategies.
Pennsylvania-based Americhanvre founder and owner Cameron McIntosh visited and consulted with the Lower Sioux on the hempcrete projects. McIntosh, one of the nation’s leading hemp experts, has participated in building and retrofitting more than 40 hempcrete homes.
He likes first to tell people that hempcrete is a “terrible” name for the material because it has few of the attributes of concrete and cannot be used for paving or structural support. As insulation, it shines. Hempcrete outperforms standard insulation by 30% to 70%, contains no off-gassing particulates, and prevents mold growth, he said.
McIntosh said hempcrete creates a blanket of uninterrupted insulation around homes, coming close to Passive House performance. Other advantages include its likely ability to sequester carbon and its qualities. “Hempcrete is completely natural,” he said. “It can push your project to carbon neutral or carbon negative with a material like this.”
The Lower Sioux approach
Desjarlais said the Lower Sioux have created a closed-loop system where the reservation grows industrial hemp for construction projects. However, the yield has not been as robust as needed, so the tribe buys from Waconia-based Hemp Acres.
The tribe plans to use hempcrete in a 60-unit development of duplexes, a new strip mall and a school, Desjarlais said.
His team delivers hempcrete as spray foam and precast blocks and panels. In all cases, hempcrete performs better than standard insulation because it has thermal mass, which “makes it 100 times better material (than standard insulation), and then you add in the fact that it’s 100% recyclable that makes like 1,000 times better,” he said.
The tribe’s work on hempcrete has generated interest in the state. Desjarlais presented to the United States Green Building Council in the Twin Cities and has provided tours of the hempcrete homes to architects, civil engineers, code officials, and others. “We’ve only gotten positive feedback from those types of people,” he said.
At least two people, one from St. Paul and the other from the Rochester area, have spoken to him about plans to use hempcrete when they build their homes.
Hempcrete projects remain rare due to continued challenges, including the need for updated building codes and more industry certifications to help material reach a wider audience.
The tribe has kept the cost of hempcrete in housing low, he said. Still, individual homeowners using it can pay a significant premium that leaves it out of reach for middle- and moderate-income households. He said that older, wealthy homeowners have constructed most other hempcrete homes.
The tribe wants to expand its current hempcrete operations by building a business to process hemp and manufacture prefabricated panels and blocks. “It could be a $30 million a year business just processing hemp for other people’s projects and selling prefabricated panels and blocks around the country,” he said.
Hempcrete uses the hurd of hemp, leaving the remainder of the plant sold in emerging markets, producing clothing, textiles, baby wipes, and toilet paper. “They say there are 50,000 uses for the hemp plant,” Desjarlais said.
Rural communities in the Midwest could replicate the Lower Sioux’s system of training members and growing hemp. “Hemp would be perfect for them to start growing and processing or building with,” Desjarlais said. “Their own community members could be rebuilding their community with hempcrete. You could do this anywhere else. It doesn’t have to be a tribal community.”
Article Credit: finance-commerce